How to Conduct an Efficient Stocktake: A Signetor Case Study
Overview
A B2B welding supplies retailer, with 10 depots, trialled Signetor’s digital stocktake solution at one location to build a business case for change. The stocked items, range from tools and abrasives to personal PPE, welding machines, and spare parts, were held in various shelving formats like palletized warehouse racking, pick bins, stock rooms, and a showroom. A small percentage of stock had barcodes printed on the boxes or outer packaging. Each location stores between 1,500 and 4,000 parts depending on local customer requirements.
Current ‘Analogue’ Stocktake Method
The existing stocktake process involved a physical paper list of items sorted by product group, which was issued to staff members to count. Counters were responsible for multiple pages of products and had to visit all storage locations to capture the total quantity. This method consumed the entire depot team’s day to complete the count and a further day inputting the results into the inventory management system. This manual approach resulted in multiple dozens of discrepancies and then a great deal of additional labour to recount and clear up the discrepancies.
Signetor Digital Stocktake Solution
The client tested Signetor’s digital stocktake solution in one depot, comparing it to their paper-based approach. To prepare for the transition to a digital stocktaking process, several enhancements were made prior to the count:
- Scannable Shelf Labels: Barcode labels were created for each product, enabling quick, accurate identification during the stocktake.
- Staff Identification: Staff badges were issued, ensuring each scan could be tracked back to the person responsible.
- Count Area Barcodes: Area-specific barcodes were created, allowing for logical divisions and more granular record keeping.
- Staff Training: Signetor trained the client’s staff in using the Zebra scanners and the revised stocktaking processes.
- Strong Audit Trail: Each scan had all the relevant information associated with it to providing a robust audit trail.
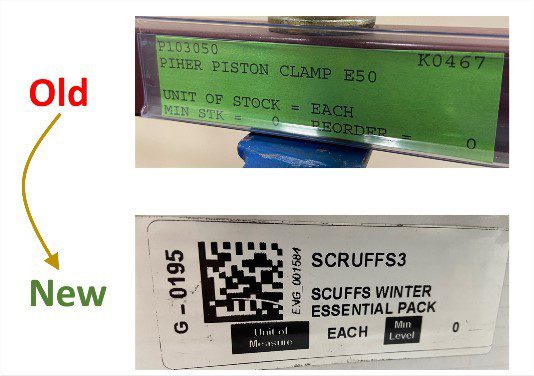
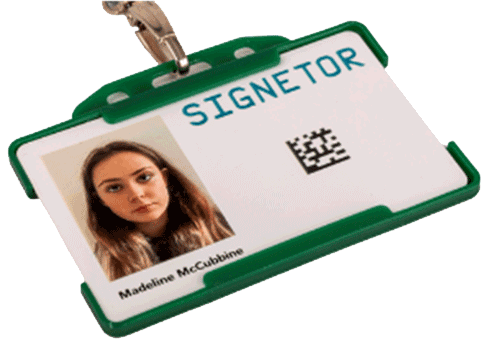
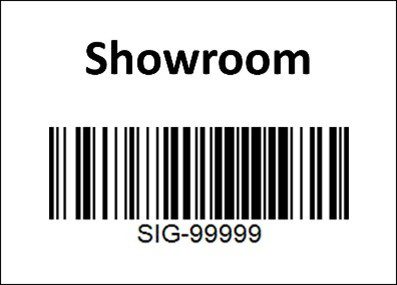
Analogue vs. Digital Stocktake Results
The digital stocktake method halved the count time and reduced the number of post-count discrepancies to a handful, allowing for more accurate inventory management and lower staff costs.
Future Business Transformation Opportunities
- Implement faster, cost-effective, and accurate stocktakes across all depots.
- Capture manufacturers’ barcodes for seamless scanning.
- Collaborate with suppliers to ensure GS1 compliant barcodes on products.
- Expand mobile scanning for better inventory control at a lower cost.
Strong Audit Trail
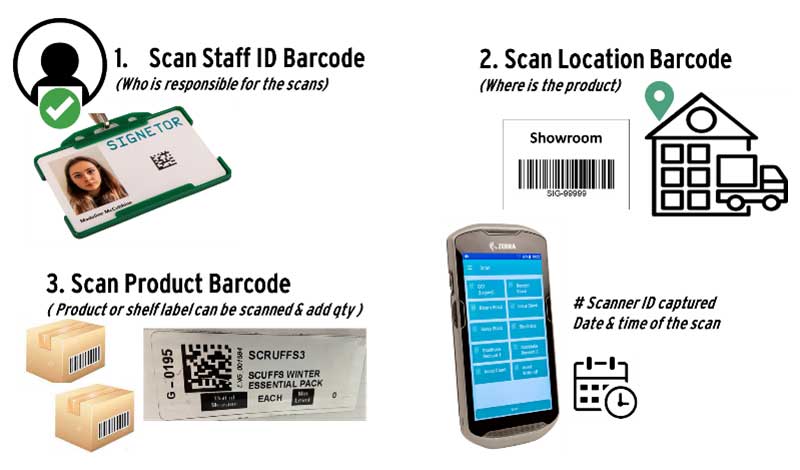
About Signetor
Signetor specializes in stocktaking, supply chain transformation, and track-and-trace programs. They offer turnkey to bespoke solutions for improved inventory control, including barcode printing, scanning hardware, software, reporting tools, system integration, staff training, and ongoing support. Signetor aims to streamline and deliver your stocktaking and inventory control needs across various sectors, such as healthcare, pharmacy, manufacturing, wholesale, and retail.