Markets Manufacturing
Keep production on track with effective inventory controls. Make better capacity planning decisions with powerful reporting
Bespoke to your manufacturing situation we deliver the right combination of solution design, technology, support and training to ensure your team can quickly and accurately manage your stock. We call this Tailored Support. Start your journey today.
Free Trial Offer
Includes use of scanner, software, training and free shipping. Try FREE for a week with no obligation!
Fancy a Chat?
We would love to talk to you
& find out how we could help.
Inventory Management
Count stock in your store areas. Divide the warehouse into logical locations, e.g. racking number.
Receipt / Issue / Transfer Stock
Maintain a record of the stock receipted, issued and transferred between suppliers, customers and your manufacturing cells. Integrate with your inventory system.
Tailored Support
Get the right level of design, technology, integration training and onsite support to deliver the best outcome.
Solutions
Case Studies
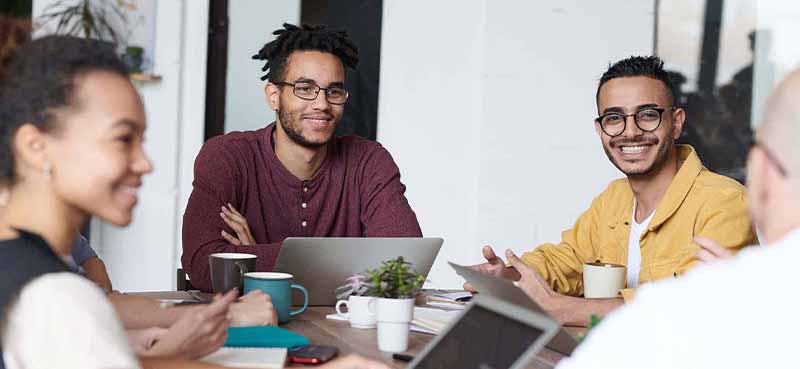
Optilogix
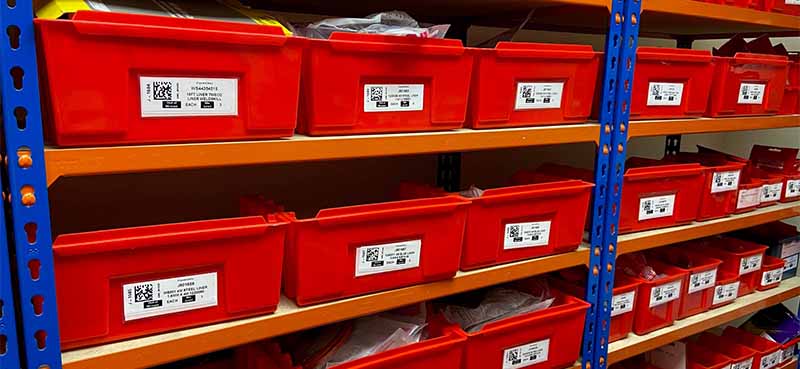
Engweld
Service Offerings
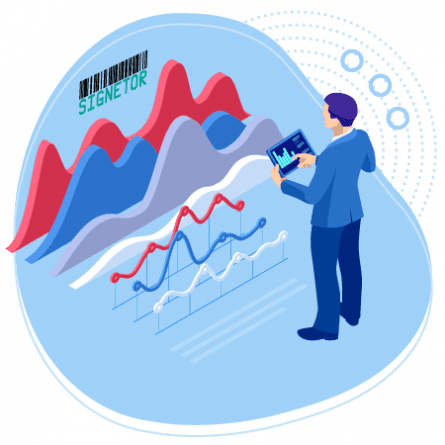
HARDWARE & REPORTING ONLY
Hardware Application Included
–––––
Remote Training & Support
–––––
Client Provides Staff
–––––
Reports as Required
£
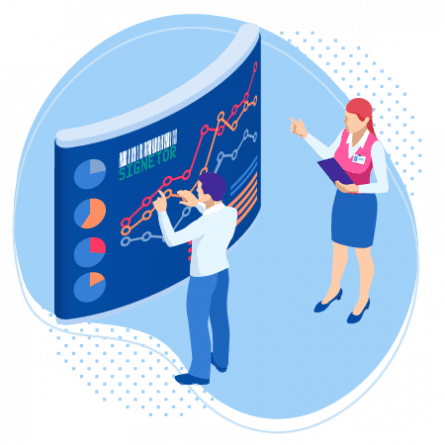
HARDWARE, REPORTING & TRAINER
Hardware Application Included
–––––
Trainer Provided
–––––
Client Provides Staff
–––––
Reports as Required
££
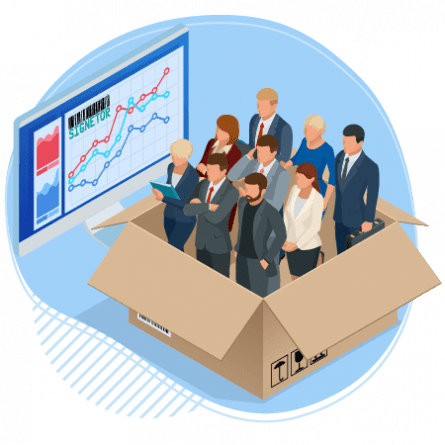
FULLY MANAGED STOCKTAKE
Hardware Application Included
–––––
Project Manager Provided
–––––
Staff Provided
–––––
Reports as Required